Pioneering electrification in aviation at scale
UK, September 1. At Rolls-Royce, we aim to lead the Advanced Air Mobility market and achieve the world’s first certification of an electric engine for commercial aircraft by the mid-2020s. Light aircraft are already flying with electric propulsion, demonstrating the technological possibilities for the decarbonisation of large aviation in the future, if we can develop at scale.
Developing the tools to support mass production
In 2022, Rolls-Royce Electrical launched a dedicated programme that will enable us to achieve the levels of mass production needed to support the industry, embedding industrialisation within our electric propulsion product portfolio.
To do this, the programme is focussed on developing the right capabilities within the business’s core functions: supply chain, manufacturing, quality and services. As such, our core industrialisation team is working in close collaboration with a new product introduction projects team to ensure that any under-development electric drive technologies and systems can be sourced, manufactured and serviced at scale.
Adapting to a large-scale mindset
Daniel Hirsch, Head of Executive PMO at Rolls-Royce Electrical is leading the industrialisation programme, bringing together and aligning each of the functional industrialisation workstreams with product development.
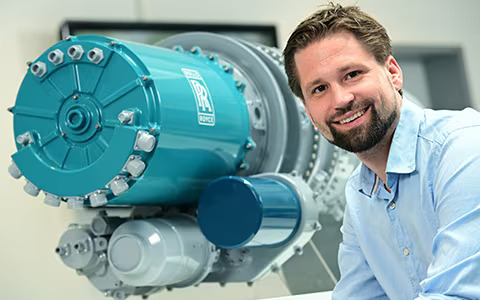
“The key challenge is to already drive the thinking towards a product that matches the high standard of industrialised aerospace without limiting us when it comes to exploring and demonstrating novel technologies. Cost and quality objectives must be met and aligned with our future supply chain. We also need to flexibly adapt concepts to customer needs and ensure we make investment decisions at the right time.”
Enabling the supply chain for Advanced Air Mobility
Our supply chain teams are responsible for sourcing partners to produce materials that will not only uphold the highest of aviation safety standards but that can be sourced and brought to the assembly line affordably and at pace, ready to support mass production.
Once chosen, the supply chain team also support our engineers by working hand-in-hand with suppliers throughout the product’s design to ensure that customer needs are met.
Matching safety with speed
Today, mass production is not a standard in the aviation industry. The volumes needed to support market forecasts for electric aviation products are more comparable with the automotive industry.
For our teams on the production line, their challenge will be to build a strategy based on speed and momentum that reaches or accedes rigorous safety requirements airframers achieve at a much slower pace.
Alongside this, our engineers are developing production techniques that minimise the number of materials used, and the amount of waste generated, supporting our pledge to become net zero by 2030.
Pace of industrialisation will be crucial
Daniel is convinced that being at the top of the industrialisation game will be a deciding factor in market success.
“We already have some of the most differentiated Advanced Air Mobility technologies to offer to the market. Now, we will need to ensure that this technology is driven to a certified product, building on highly efficient, available and sustainable manufacturing processes, backed by a capable and resilient supply chain, and that the product comes with a future-proof service offering and network. This will be the key to sustainably maintaining market leadership for electrical power and propulsion systems in aviation in the long run.”